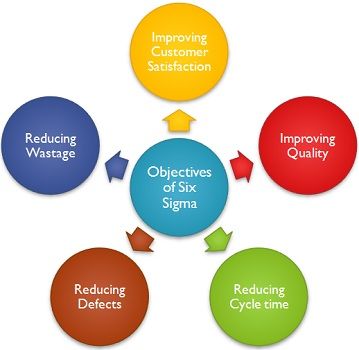
www.gmsisuccess.com
The nature of business has changed dramatically since the late 1980s when the United States’ lead in productivity was subjected to increasingly direct foreign competition from Asian and European industries. The American response to these challenges has been twofold. First, industries in the United States have moved production of less-complex standardized goods to foreign plants or, in many cases, seceded such low-profit manufacturing to developing nations. The net effect of such actions has been an unprecedented increase in the size of the service sector and a concentration on high-valueadded manufactured products.
Currently, the service sector, defined as private nongoods-producing industries, accounts for approximately 70% of total economic activity in the United States. Services can include warehousing, transportation, distribution, and sale (rather than production) of a good, or they may involve the provision of a service such as medical care or the preparation and serving of restaurant meals. Second, American industries have found that they must maintain a sustained focus on quality in the production of goods and services in order to be globally competitive.
The American Society for Quality Control defines quality as “the total features and characteristics of a product or a service made or performed according to specifications to satisfy customers at the time of purchase and during use.”
1 These two continuing trends—the rise of the service sector and the increased focus on quality—challenge the traditional role of the cost accountant, who historically was trained to track and cost out mass-produced standardized items. In addition to expertise on production and costing methods, today’s successful management accountant must have in-depth understanding of service quality. To ensure maximum productivity, profitability, and quality of complex tangible goods and intangible services, companies are using the sophisticated Six Sigma business management strategy. Much has been written about the Six Sigma methodology and its contribution to improving business processes. For example, Michael L. George discusses how to select projects that can be improved to deliver the maximum value with the least effort.
2 Jay Arthur focuses on methods to dramatically improve speed and quality in manufacturing as well as service organizations.
3 Unfortunately, most authors fail to discuss the crucial role that management accountants and accounting consultants can play in the successful adoption and use of Six Sigma methods. These require a team effort utilizing experts from a variety of disciplines, and we believe that management accountants, with their expertise in problem solving, should be key players on any Six Sigma team. To demonstrate these possibilities, this article will consider how management accountants can become involved in the five phases of the Six Sigma process as applied to service industries in particular. To aid in understanding how management accountants might contribute to a Six Sigma team, we will first discuss how service providers can use Six Sigma methods to improve their operations. As a case study, we will present research on the potential use of such techniques to improve the U.S. Army supply warehouse system.
We will then consider how management accountants can become involved in the five phases of the Six Sigma process in the service industry as either team leaders or key team players.
BACKGROUND ON THE U.S. ARMY SUPPLY SYSTEM AND SIX SIGMA :
The current missions in Iraq, Afghanistan, and Kosovo, as well as other humanitarian logistics operations in which the U.S. military has an increasing role, require highly efficient distribution, warehousing, and business processes. To maximize the readiness of tactical units, Supply Support Activities (i.e., the activities of direct support supply units, missile support elements, and maintenance support units) must be highly effective, ever reducing customer wait times and improving quality
The goal of Lean Thinking is to increase efficiency within an organization by eliminating defects and minimizing variation in every product, process, and transaction. Examples of defects in a warehouse include delivering a part in 15 days when a customer is promised receipt in 10 days or an inventory accuracy of 94% when the goal is 97%. Variation can be applied to any activity that can be measured, such as delivery times, weights, inventory counts, performance scores, etc.
Processes with more variation are typically not as efficient as processes with less variation. One of the primary methods for instituting Lean Thinking is the utilization of Six Sigma methodology.
Sigma (s) is the Greek symbol used to represent the standard deviation for a set of measured data. If data are represented as a bell curve distribution, then distances from the midpoint of the distribution can be measured in terms of Sigma. Sigma levels are used to describe how well the variation in a process meets the customer’s requirements.
What the customer wants is used as the standard mean, and not meeting the customer’s needs is described as a defect. Sigma is therefore defined as the standard deviation of a process in statistical control. The quantitative goal of the Lean Six Sigma program is to obtain six times the standard deviation between the mean process and the closest tolerance limit. Implementation of Six Sigma creates a process capable of producing only 3.4 defects per million opportunities. The Department of Defense warehousing operations offer an excellent case for assessing the potential use of Lean Six Sigma methodology
IMPROVING ARMY WAREHOUSING OPERATIONS WITH LEAN SIX SIGMA:
Selecting the Project. The first step in effective application of a Lean Six Sigma process is selecting projects that can be improved to deliver the best value with the least effort. There are two basic methods for project selection, both of which have benefits and drawbacks. The first method is the top-down approach, which uses input primarily from top management who view failure as gaps between strategic initiatives and actual performance. This method ensures commitment from upperlevel management but may not provide enough detail about defects and their underlying causes to clearly determine the need for Lean Six Sigma methods. In contrast, the bottom-up method involves soliciting ideas from both upper management and lower levels in an organization. Ideas gleaned from this method are screened and grouped in order to identify opportunities for specific Lean Six Sigma projects.
An advantage of the bottom-up method is that a larger group is allowed to participate, which provides a variety of project ideas. The drawback of this method is that some project suggestions might not be supported by data or be compatible with strategic goals. Regardless of the method used to generate ideas, all potential projects should undergo goal-congruence evaluation and cost/benefit analysis. Projects must be congruent with the mission, strategic goals, and objectives of the organization, and the financial and nonfinancial benefits must outweigh costs of the project.
Potential projects not meeting these criteria should be eliminated. The remaining projects are possible candidates that should be researched further by the Lean Six Sigma team. In the case of DoD supply chain management, the most crucial link is local warehouse operations. The U.S. Army personnel who are most knowledgeable about warehousing operations are its Quartermaster Supply Technicians, the warrant officers who manage Army warehouses. These U.S. Army Quartermasters have extensive knowledge about the causes, effects, mitigation, and remediation of errors in warehouse operations. Therefore, the most efficient approach to pinpointing problem areas and opportunities for specific projects in military warehouse operations is the bottomup methodology. We have used a survey of U.S. Army Quartermasters as the basis for identifying problems in the warehouses and the probable causes of those problems.5 According to these managers, customer complaints concerning local warehouse management was the primary problem. Once a significant problem has been pinpointed, that process must be improved.
In Lean Six Sigma, the DMAIC model is the recommended approach. It is a five-stage methodology that consists of “Defining, Measuring, Analyzing, Improving, and Controlling” a project. In the next section we explain how each stage might be applied to improving customer satisfaction for a hypothetical U.S. Army warehouse.
THE IMPORTANT ROLE OF MANAGEMENT ACCOUNTANTS :
The intent of this study is to demonstrate how management accountants can and should be team members or team leaders in each step and phase of a Lean Six Sigma project. To this end, we will examine the crucial role management accountants can play in the projectselection step and the five phases of the DMAIC process, referencing the hypothetical Army warehouse operation. Selecting the Project. Project selection is the most important step because all other actions are dependent on which problems and opportunities are addressed.
Management accountants are particularly suited to either direct this phase of the Six Sigma process or provide crucial support as team members. In the Army warehouse case, we used a bottom-up approach to problem definition. This approach is almost identical to the consultative manner in which management accountants develop participative budgets for their yearly operational budgets and plans. In bottom-up participative budgeting, management accountants use the input of lower- and middle-management employees to derive estimates for their master budgets.
Management accountants know that, while this approach is timeconsuming, it enhances employee motivation, communicates goals and performance levels to the employees, and ensures that employees understand and accept corporate goals. Most management accountants have extensive experience soliciting information from employees at all levels, developing plans from that information, and providing feedback about variances from actual versus expected performance. Management accountants working with managers and company engineers are therefore ideal candidates for directing a bottom-up Six Sigma survey study.
In some cases, it may be more appropriate to use a top-down approach to project selection, especially when there are time constraints or the problems to be addressed are highly complex and require expert knowledge. In these situations, a top-down approach to problem definition may be the best course of action. The top-down method can effectively identify processes with unacceptable performance variation and develop projects to improve those processes. Statistical analysis also can be used to identify processes with unacceptable variation. Then a cost/benefit analysis may be performed to determine the potential net benefits of improving that process.
This analysis requires comparing the profitability generated by relevant business segments, products, and customers within that process with the costs of meeting the needs of the customers. Customer needs can be evaluated with reference to surveys, warranty information, and other satisfaction indicators. Once net benefits of improving a process are determined, a process analysis can help develop specific projects for improving that process.
Again, management accountants have experience in this type of information solicitation based on previous interaction with managers and executives regarding strategic issues such as capital project evaluation, plant acquisitions and divestments, segment performance, value stream analysis, and product life-cycle profitability.
In summary, experienced management accountants have the expertise and knowledge of their company required to direct the all-important problem-defining phase of a Six Sigma project. As noted earlier, the Army warehouse project involved customer complaints about timely delivery of supplies. In this case, management accountants would have been highly qualified to interpret the results of Quartermaster surveys, for example, to determine the best project.

No comments:
Post a Comment